グループB規定は、カンブリア大爆発を引き起こした!
1983年、FIAはグループB規定を緩和し『連続する12か月間に200台製造された車両を市販車としてFIAが認定すれば、20台を正常進化車(EVOLUTION)としてラリー選手権へ参戦できる』 この規定を最大限広くとらえた多くのカーメーカーが参戦することになり、グループBでのラリー選手権は実質限りなくプロトタイプカーに近い車両で戦われることになった。多くのカーメーカーが参戦を準備し始めた。
まさに、『メカ4WDラリー車のカンブリア大爆発である!』
FR4WDラリー車は、競合他社に打ち勝つために、更なる性能向上が必須であった。エンジンの性能向上、足回りの軽量化、そして、駆動系の軽量化である。駆動系の軽量化として、2つのアイテムを取り組むことが承認された。
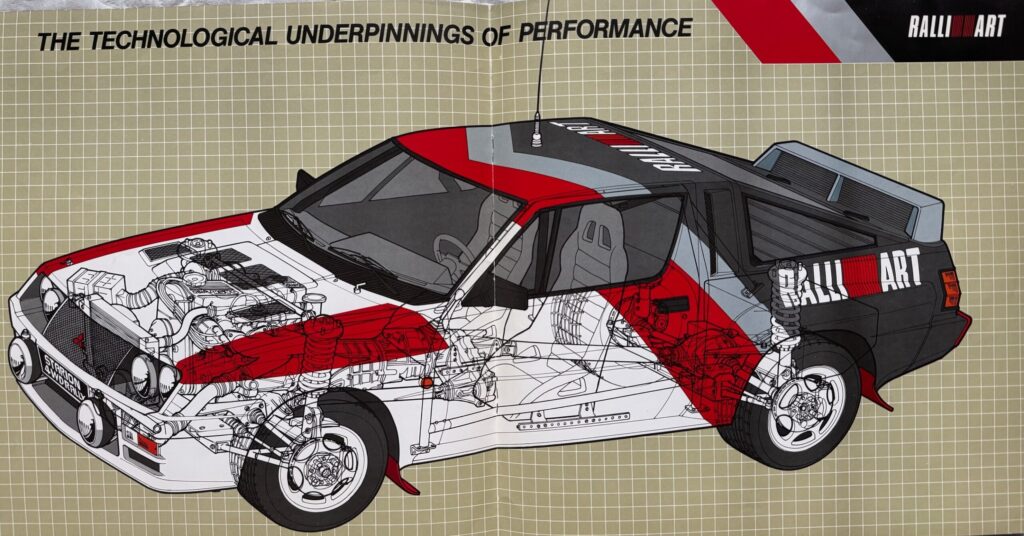
スタリオン4WDラリー車
【その壱】 前後デフキャリアのアルミ化
駆動系部品は、鉄の塊である。鉄系の比率が多い。強度と剛性が両立できるコスパの良い材料である。
全ての構成部品を鉄系からアルミ系に変更できれば、重量は、1/3が期待できる。現実は、とても無理で、筐体(ケース)類のアルミ化程度である。自社でアルミ化筐体を適用した実績を調べる。先輩のアルミ化筐体の資料があったが、検討のみであった。次に他社調査をする。いくつかの実例はあった。 日本では、ラリー競合メーカーがFR2WDリヤデフキャリアで適用していた。有名なラリーカーである。外観画像は入手できたが、詳細は分からない。
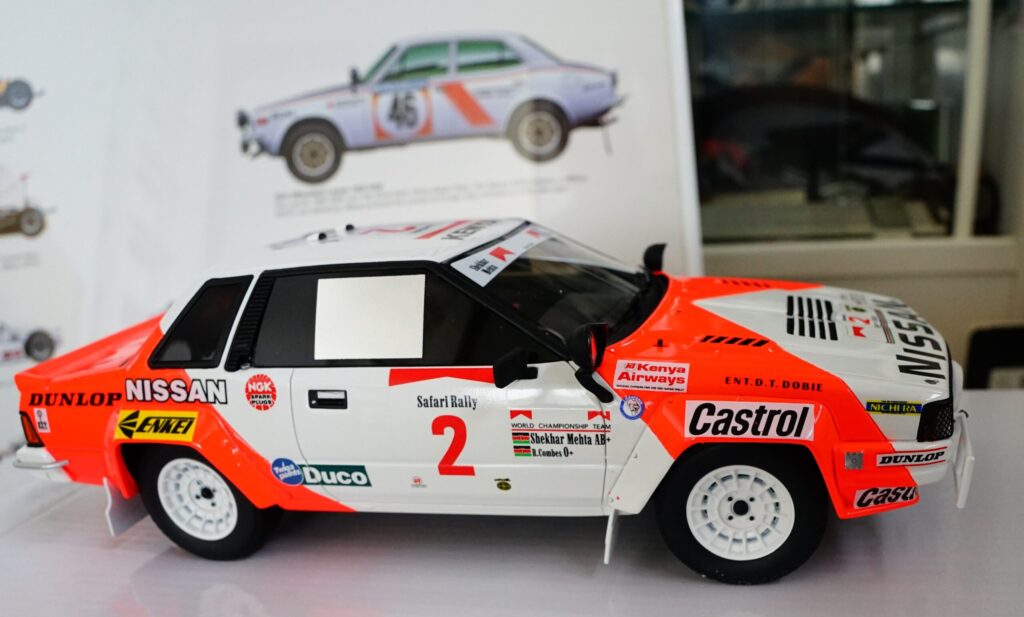
NISSAN-240RS (ミニカーコレクション)
軽量化の常套手段。それは、鉄をアルミへの材料変更…
アルミを使う理由は、軽量化と熱伝導率の良さであるが、鉄とアルミの熱膨張率が異なるので、温度変化に注目である。ベアリング外輪との嵌め合い変化やプレロード変化が大きくなる。この懸念点を考え設計した。
たかが20台のスペシャル部品である。鋳鉄で設計したデフキャリアの図面の材料欄をアルミ鋳物に変更すれば、作業終わりとなる。でも、そんなのは設計とは言えない。許せない。頭の中で創造の玉が光り回りだす。でも、時間は無い。今みたいにCAE解析が簡単にできない時代。鉄とアルミの剛性差を補正するには、筐体肉厚を増やす必要がある。すると、重量減少比率は、1/3から1/2へ目減りする。
使うのはラリー車である。ラリー車の神様は、重さに厳しい。ラリー車に多くの部品が付けられるが、完成後、自分の目で見て、ナットから飛び出したねじは、すべて切り落とす。1個あたり数ミリグラムの減肉かもしれないが、ラリー車すべての飛び出したねじ先を集めると数kgも重量低減につながる。神様は、地道な努力でサファリラリーを勝利に導いた成功体験を持っていた。ラリー車の神様をごまかすことはできないし、適当な仕事はしたくない。どうすればいい?鉄キャリアとアルミキャリアの剛性差を実体で計測するには、高ねじりトルクを入力可能な試験設備と試験部門の工数が必要である。たった、20台の開発のために量産開発している部門がボランティアで協力してくれる訳がない。
好きなラリー開発に想いをこめることはできるが、物質的に証明する手段と結果を手にする必要がある。まさに量産開発に対する高い壁にぶつかったのである。
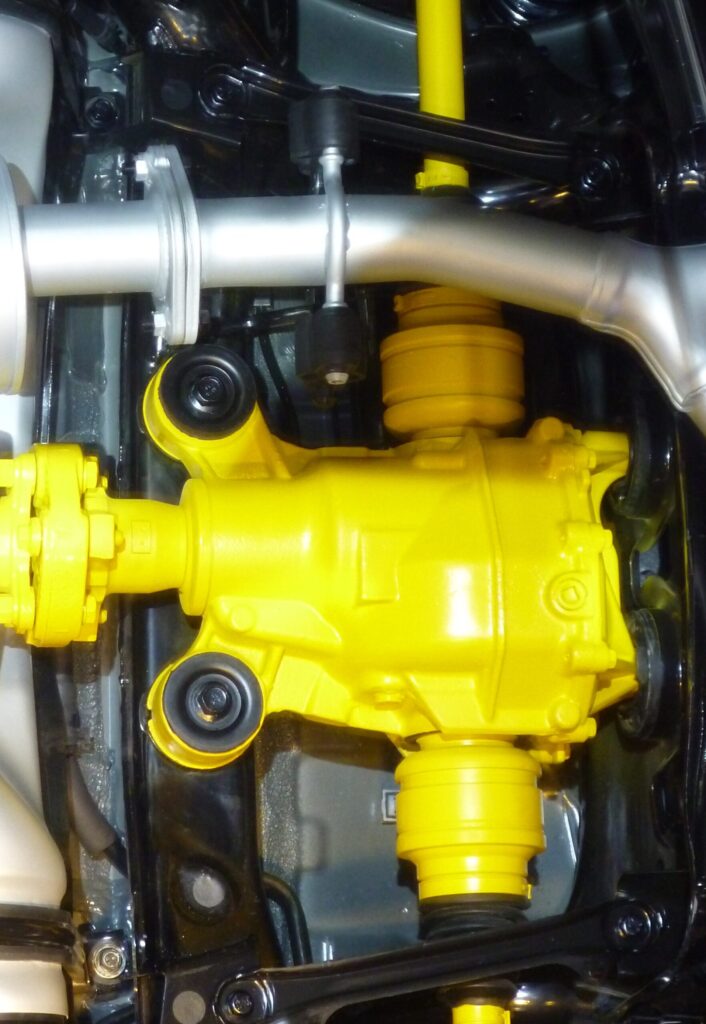
リヤデフキャリア(2014北京モーターショー調査画像)
困ったときの神頼み…それは、閃き_💡_『直観』とも言う
『困ったなあ~』
打開策を考える。時間もないので寝ている間に頭に閃いた方法を信じて行動開始である。
【行動_その壱】
材料技術部にアルミと鉄を簡易的に実体の剛性を計測できる方法が無いか?問合せてみる。
【行動_その弐】
購買部へアルミデフキャリアの製造を経験したことのある
サプライヤーを探してもらう。
同時に動いた。すると、どうであろうか!
材料技術部からも購買部からも同じ回答が来た。
『当方懇意のサプライヤーが全面協力してくれる。』
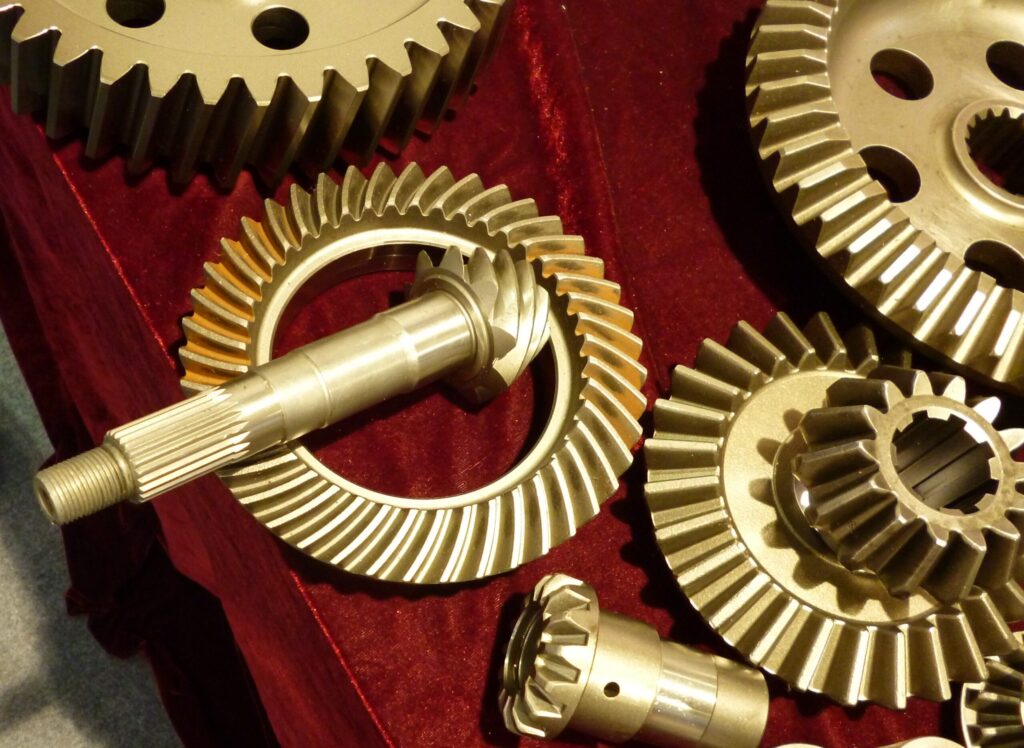
ハイポイドギヤ(2014北京モーターショー部品館調査)
青天の霹靂…世の中は広い。いろんなことを考えるエンジニアがいるもんだ…
エンジニアを伴いサプライヤーが来訪した。材料技術部同席の中、事前に伝えておいた当方希望に対する回答を説明した。
●ヤング率を材料の1万分の1に調整した特殊な発泡スチロールでデフキャリアを製作する。
すなわち、計測する歪が1万倍に増えるので、逆に軽荷重で大荷重下相当の発生応力を計測できる。短時間で実体試作品を製作しなくても、特殊材料のモデルを使って最適形状および最適肉厚を選定できる。特別に開発した発泡スチロール材料なので、計測結果から簡単にモデルを形状変更して評価できる。この手法の開発に四半世紀を要したとのこと。努力の賜物である。CAE解析(デジタル)がまだまだ特殊な時代に、まさにアナログで確立したこの手法をとっても微笑ましく受け入れることができた。じぶん自分は、やっぱり、アナログ時代のエンジニア、いや、カンジニアだなあ~
ただ、テクニックが必要である。テクニックとは、接着方法と接着剤タイプ、歪ゲージの接着テクニックである。 歯車や軸、ベアリングは、バルサ材で作る。あくまで、筐体の剛性比較であり、剛体にして歪の影響を省く。目の付け所が良い。
『求めていた内容です。試作をお願いします。』
特殊モデルが完成したとの連絡を受け、サプライヤーを訪問した。鉄鋳物やアルミ鋳物を主体とした生産工場に開発部門も同居している。粉っぽい空気感に包まれ、試験場へ案内された。試験装置に吊り下げられたユニット。宙に浮いている。要所要所に貼り付けられた歪ゲージから色とりどりのケーブルがペーパー記録計につながり、血管模型のように見える。
歯車噛合い点に微少な力を作用させる。実機と同様に、応力集中する箇所や高応力の箇所がデータ化していく(アナログ時代のペーパー記録計)。鉄のモデルとアルミのモデル。記録計に蓄積されたデータを変換すると、見事に応力分布図が完成した。
実は、鉄の筐体での入力vs応力データを持参していたので、参加者でデータを比較してみると、補正係数を加算することで、ほぼほぼ相対比較できた。
『この手法は有効です。今回のデフキャリヤに限らず、多くの駆動系アイテムに応用できます。』
その後、この手法でアルミ鋳物形状を固定し、試作型で鋳物素材を鋳造した。内部加工で仕上げ、歯車類を組み込んで、アセンブリとして完成した。重量低減量も目標達成した。
ラリーチームへ引渡し、アルミデフは、ラリー車試験へとステップを進めた。
この手法を使い、その後のオフロード4WD用フロントデフキャリア(鋳鉄)を極限まで軽量化した。 新型SUVモデルに目玉駆動系アイテムとしてアイテムとしてエントリーした。
サプライヤーの努力の賜物ではあるが、『餅は餅屋』と割り切り、カーメーカーは上位ユーザー目線で開発して量産につなげるのも、自動車会社としては大切である。また、サプライヤーにとっても、売り上げ向上につながる。
まさに、『ウィンウィン(Win-Win)』のひとつとして経験した事例であった。
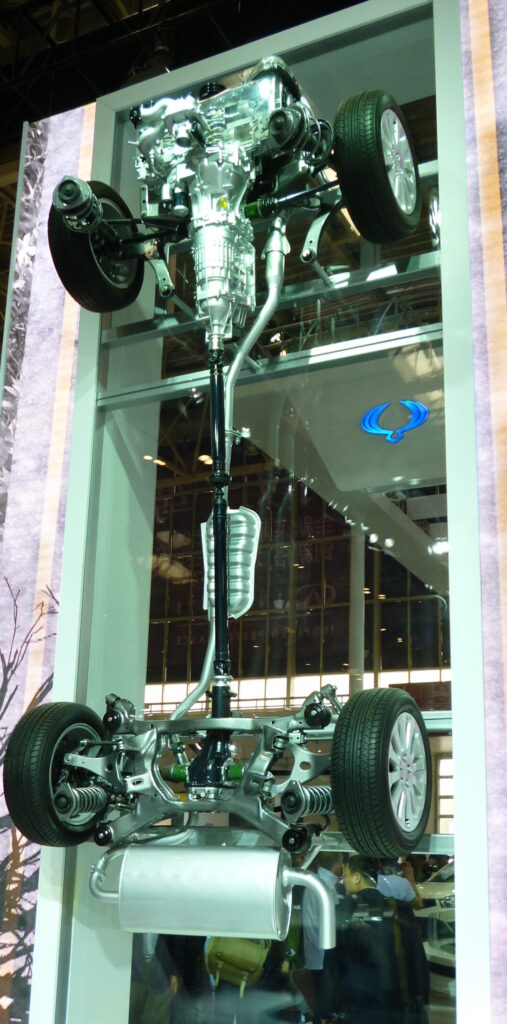
4WD 展示モデル(2014北京モーターショー)